Jet Impact on the Underside of a Superhydrophobic Surface
2018
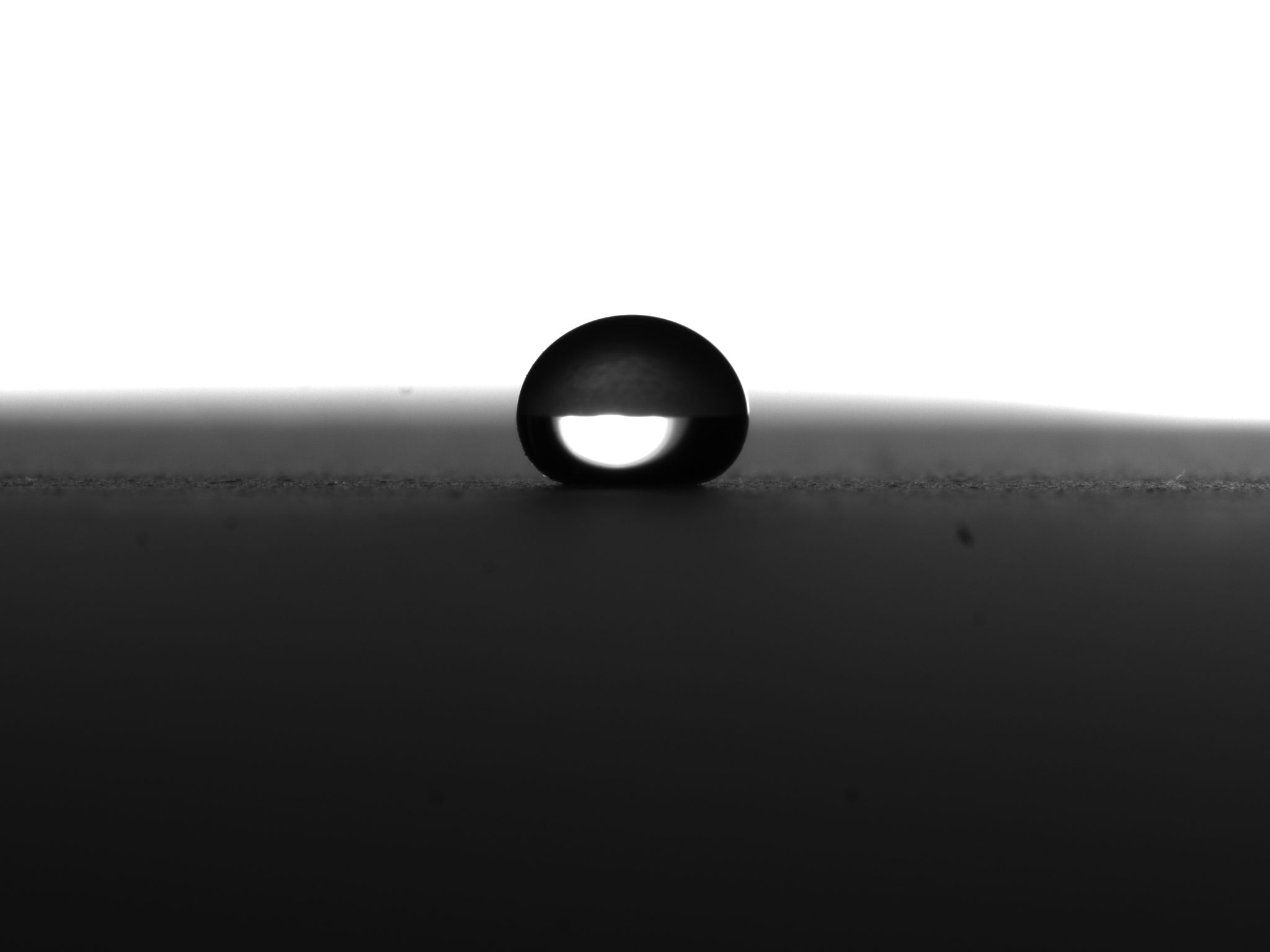
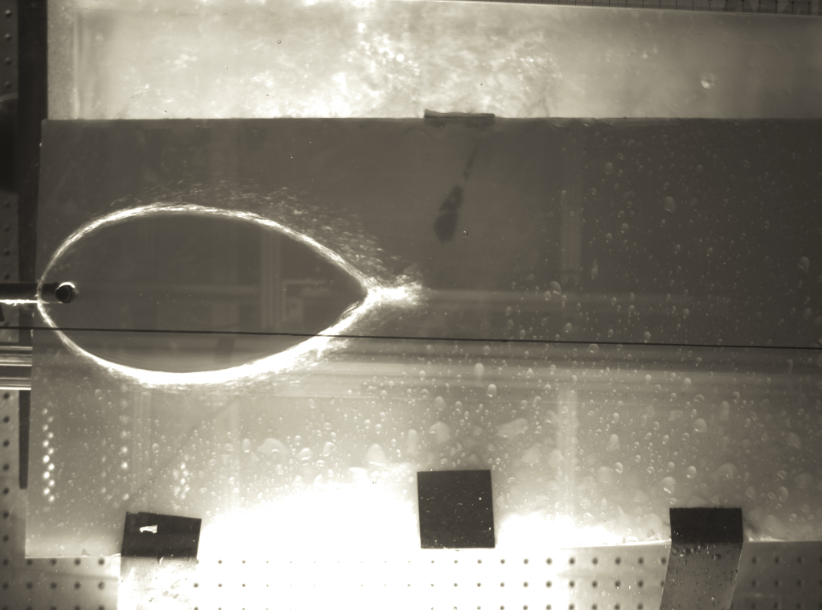
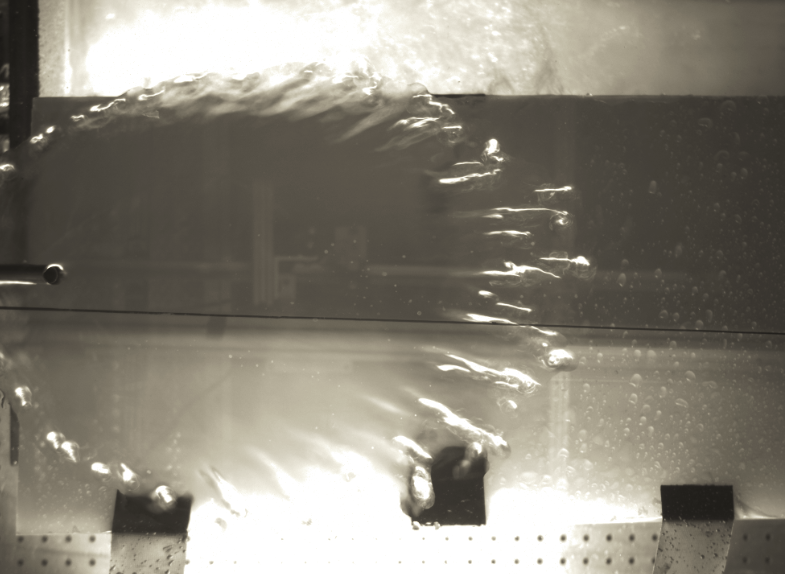
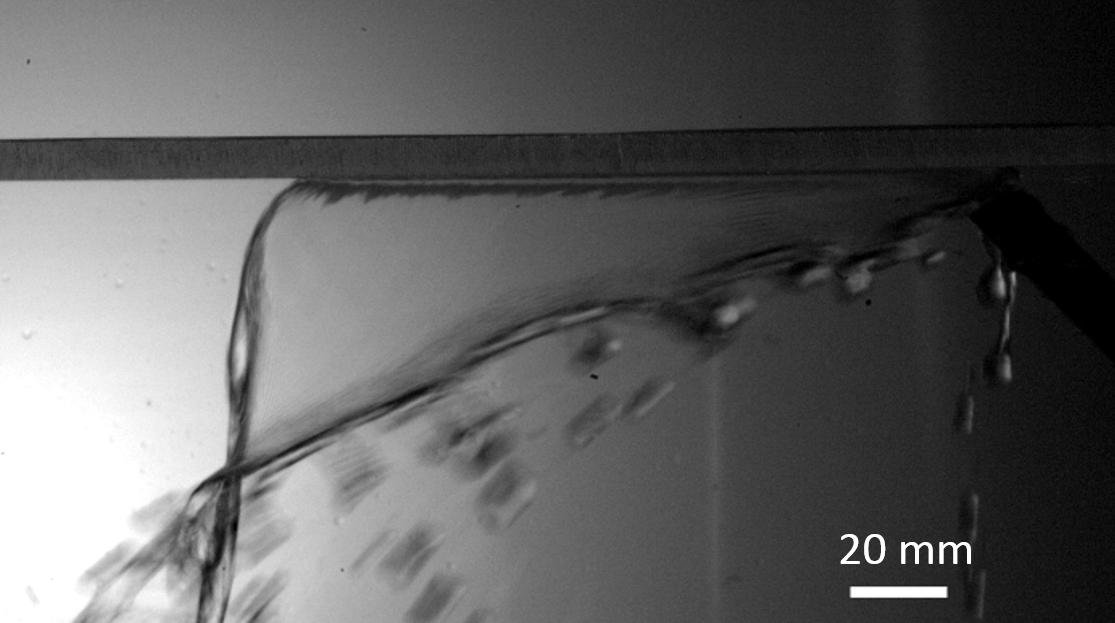
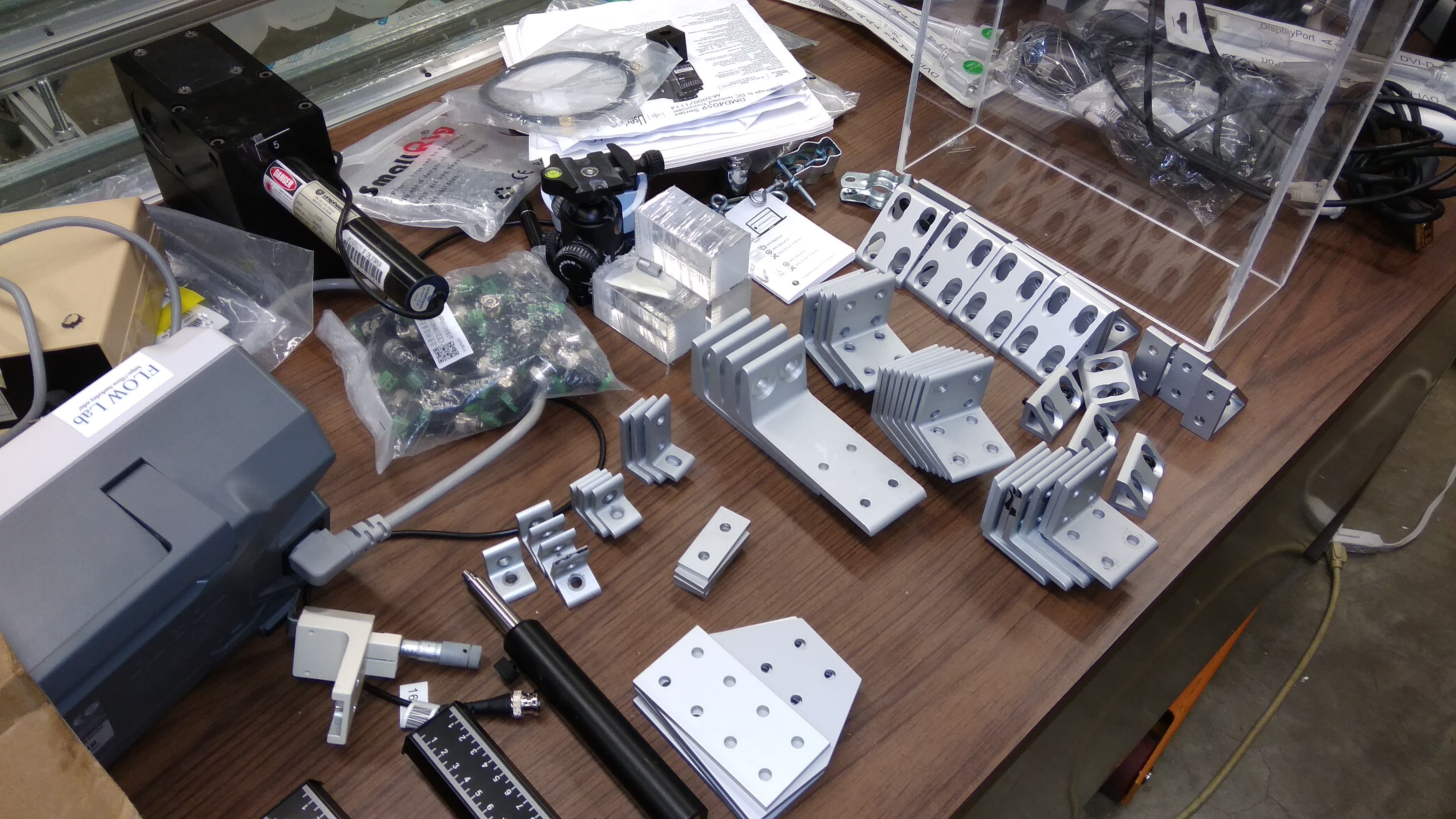
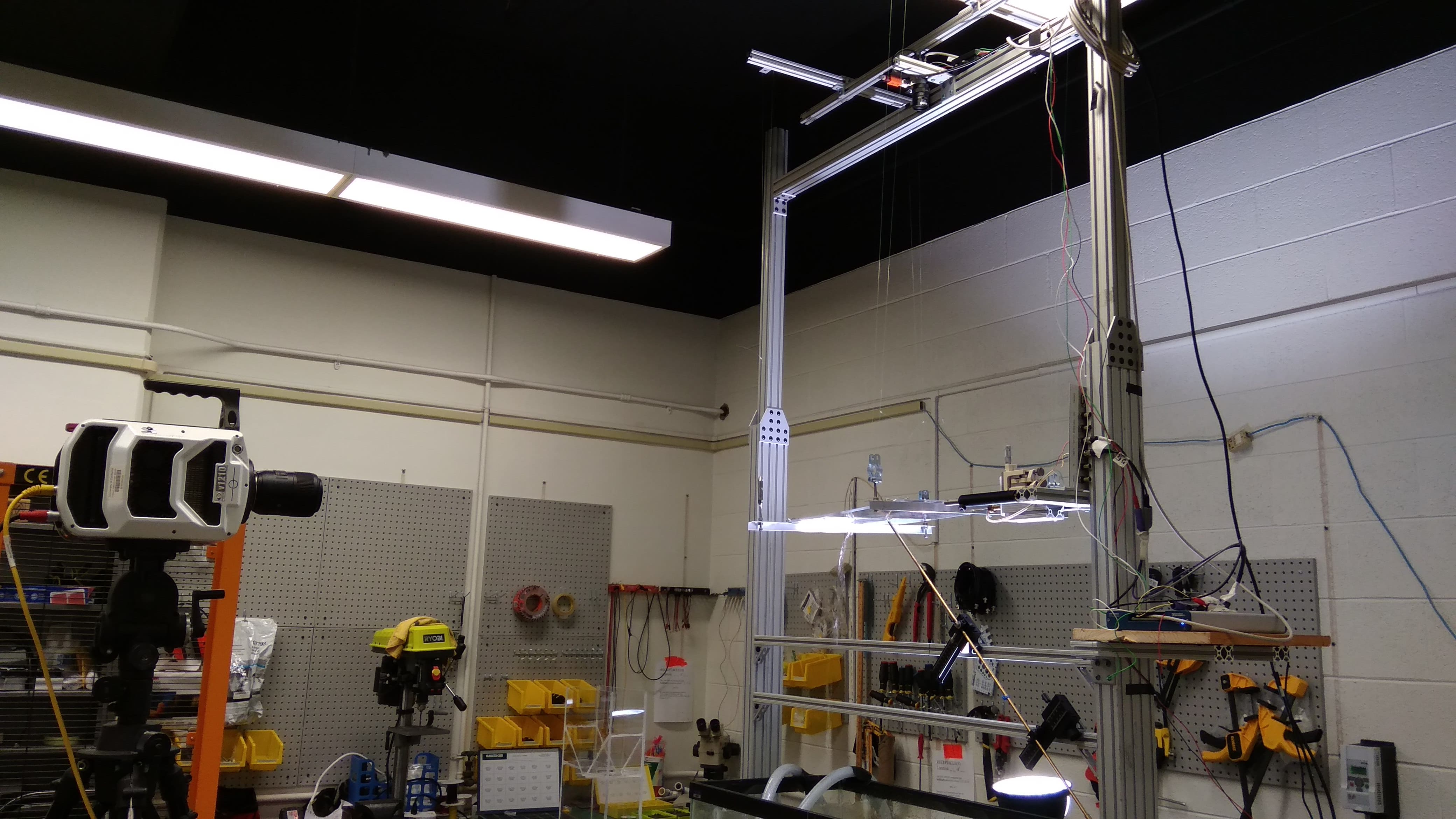
Air lubrication for drag reduction has been long considered as a way of reducing drag in marine vessels. It consists on creating a thin air layer between the boat’s hull and the water by pumping high pressure air underneath the boat. Since the viscosity of air is much lower than that of water, this air layer creates a lubrication film which effectively reduces the friction between the water and the boat. Along with this reduction, multiple benefits are obtained: less fuel consumption with its economic impact, lower negative atmospheric emissions, increase of speed, lower bulk of fuel on board etc.
Nevertheless, pumping air at high pressure under the hull requires some additional energy, and thus, the net savings come as a balance between this energy used and the drag reduction attained. Furthermore, air layers underwater are inherently unstable: the continuous air film tends to break apart into multiple bubbles before leaving the hull and rising to the surface
Simo Mäkiharju realised that by covering the surface of the ship with a water-repellent (super-hydrophobic) material, the air required to establish a continuous air layer reduced considerably. During the nine months of my MSc Thesis at his lab (FLOW Lab) at U.C. Berkeley, we studied the mechanisms (the reasons why) such coating helped reduce the air required to form a stable air layer, decreasing the energy need to pump it underwater, and increasing therefore the net energy savings.
The research was divided in two main fronts:
1) First, we tried to understand numerically how the interface between air and water behaved and caused the rupture of the air layer. This interface is wavy, similar to a sea full of waves, but with much smaller size. We simulated it with a simple numerical membrane model: the water-air surface tension acted as the elastic force that keeps the membrane straight, and the pressure variations due to the turbulent flow in the water and air layers moved the membrane up and down. We obtained a turbulence sample from the Johns Hopkins Turbulence Database which, after proper scaling, allowed us to observe how some of the water waves were high enough to impact and wet the ship’s hull.
2) Second, we tried to build an experiment (see in the images) that represented the impact of water on the underside of a hull, as we had seen in the simulations. The result was conclusive, showing that the area wetted and the time water spent in contact with the surface were several times smaller if the surface was coated with a super-hydrophobic material.
This allowed to better understand the phenomena and the relevant parameters of a technology that could reduce consumption and pollution produced by marine vehicles. Find the MSc Thesis Report and a published paper in the Journal of Fluid Mechanics below