Wind Aerostructures FS Team Delft
2016
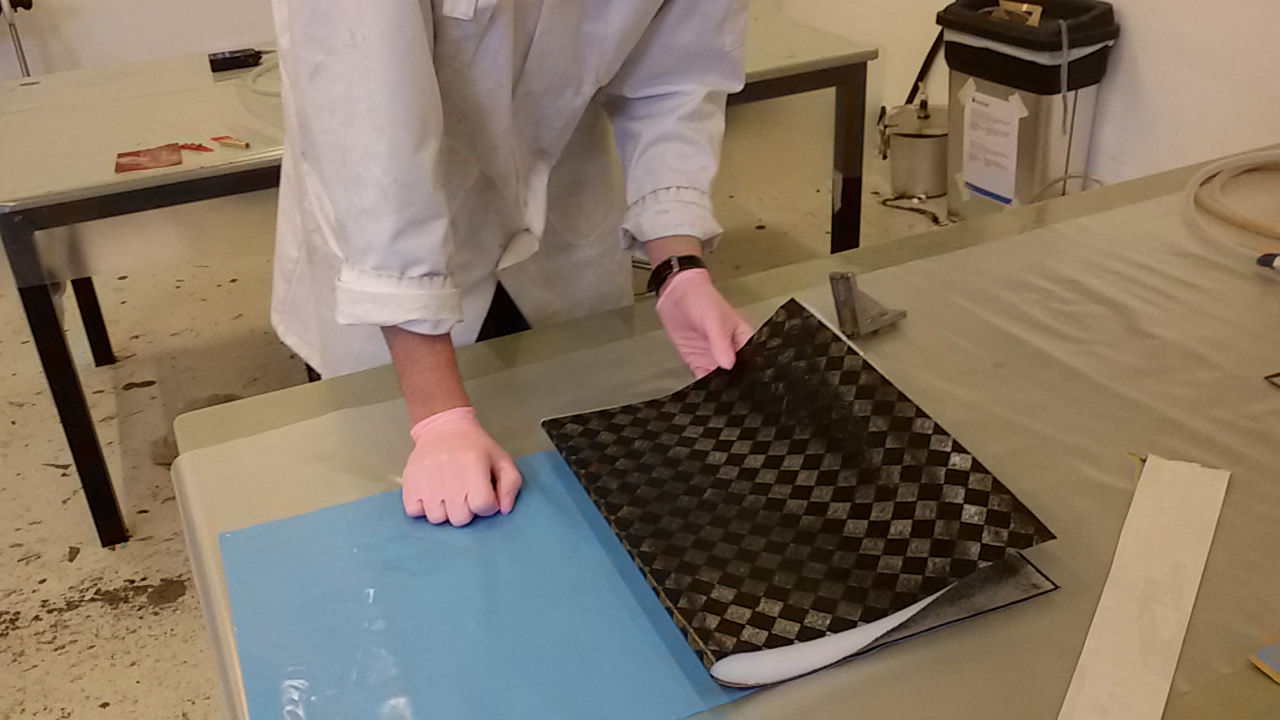
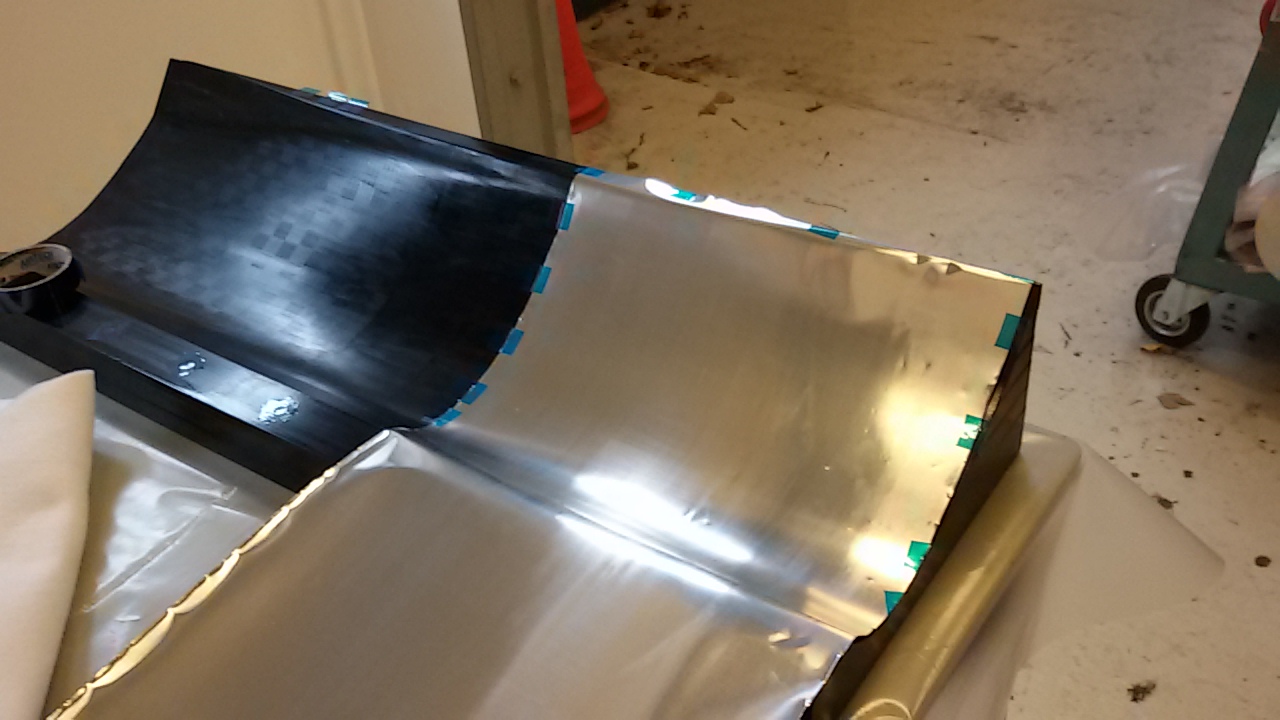
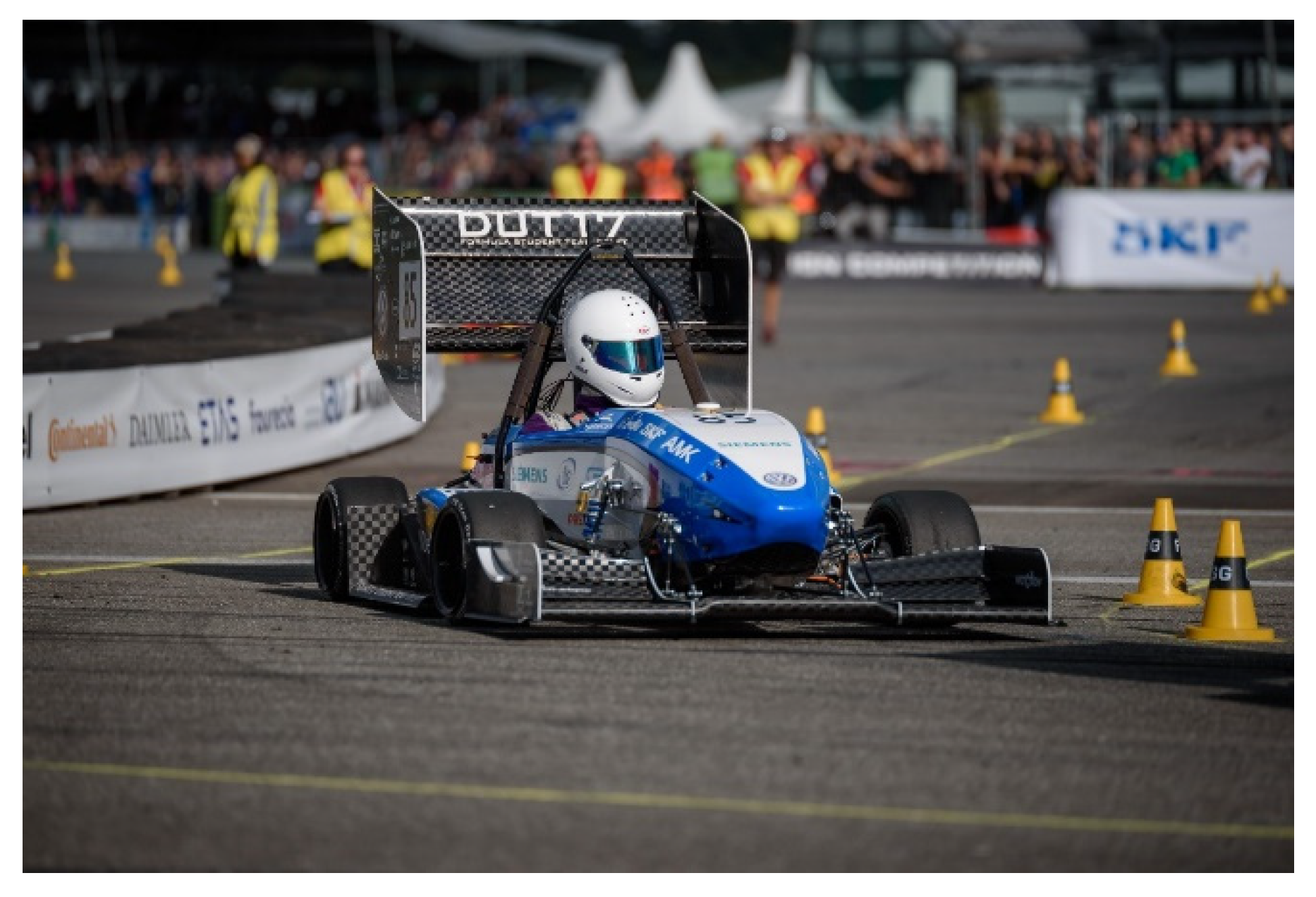
After the two years spent in the Formula Student Team of the Universidad Politecnica de Madrid, UPM Racing (see wings and bodywork projects), I moved to the Netherlands, Delft for the Aerospace MSc. TU Delft hosts one of the best Formula Student teams on the world (Formula Student Team Delft), and thus I applied to join.
After a couple of interviews, a colleague and I were assigned to the structural design of the front and rear wing. The wings are usually made of a nucleus of foam covered by epoxy-resin-preimpregnated (prepreg) carbon fiber. The process consists on milling the foam to the shape of the wing (a bit smaller actually), covering it with the carbon fiber fabric, close two moulds (one upper and one lower) and heating and making a vacuum around all the assembly.
This process, however, required the construction of two molds (expensive and time-consuming), and left some accumulation of resin where the upper and lower molds joint. Similarly to when there is too much soup in the lunchbox and a small quantity spills when closing the lid. This was aesthetically not pleasing, but furthermore deteriorated the air flow from the leading edge (front tip) of the wing.
We investigated a new process, inspired on the icelandic team Spark, in which one of the molds was removed and a thin aluminum sheet was wrapped around the carbon fiber. Such method had the advantage of requiring only one mold as well as leaving the leading edge of the airfoil clean.
This new approach nonetheless proved to work only in simple geometries (mainly 2D extruded wings), since on more complex, twisted elements the aluminum sheet wrinkled easily and produced accumulations of resins. Despite these problems, all the simple wing airfoils (front main element and all rear wing) were manufactured with these new method, saving the team half of the time and cost of the molds’ production.